What is Brass
Author : Admin Posted Date : 12/16/2016 1:05:49 AM
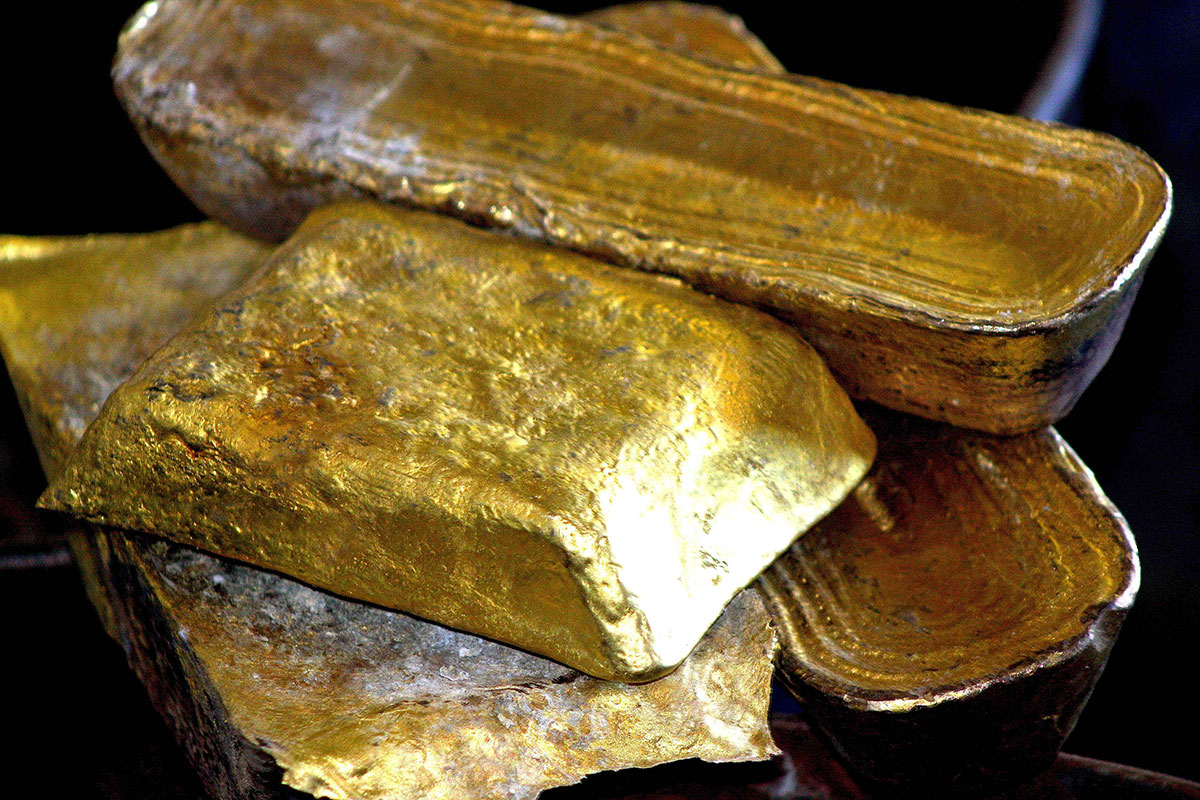
Brass is a metal alloy made of copper and zinc; the proportions of zinc and copper can be varied to create a range of brasses with varying properties. It is a substitutional alloy: atoms of the two constituents may replace each other within the same crystal structure.
By comparison, bronze is principally an alloy of copper and tin. However, bronze and brass may also include small proportions of a range of other elements including arsenic, phosphorus, aluminium, manganese, and silicon. The term is also applied to a variety of brasses, and the distinction is largely historical. Modern practice in museums and archaeology increasingly avoids both terms for historical objects in favour of the all-embracing "copper alloy".
Brass is used for decoration for its bright gold-like appearance; for applications where low friction is required such as locks, gears, bearings, doorknobs, ammunition casings and valves; for plumbing and electrical applications; and extensively in brass musical instruments such as horns and bells where a combination of high workability (historically with hand tools) and durability is desired. It is also used in zippers. Brass is often used in situations in which it is important that sparks not be struck, such as in fittings and tools used near flammable or explosive materials.
Properties
Microstructure of rolled and annealed brass (400X magnification)
Brass has higher malleability than bronze or zinc. The relatively low melting point of brass (900 to 940 °C, 1652 to 1724 °F, depending on composition) and its flow characteristics make it a relatively easy material to cast. By varying the proportions of copper and zinc, the properties of the brass can be changed, allowing hard and soft brasses. The density of brass is 8.4 to 8.73 g/cm³ (approximately .303 lb/cubic inch).
Today, almost 90% of all brass alloys are recycled. Because brass is not ferromagnetic, it can be separated from ferrous scrap by passing the scrap near a powerful magnet. Brass scrap is collected and transported to the foundry where it is melted and recast into billets. Billets are heated and extruded into the desired form and size. The general softness of brass means that it can often be machined without the use of cutting fluid, though there are exceptions to this.
Aluminium makes brass stronger and more corrosion-resistant. Aluminium also causes a highly beneficial hard layer of aluminium oxide (Al2O3) to be formed on the surface that is thin, transparent and self-healing. Tin has a similar effect and finds its use especially in seawater applications (naval brasses). Combinations of iron, aluminium, silicon and manganese make brass wear and tear resistant.
Lead content
To enhance the machinability of brass, lead is often added in concentrations of around 2%. Since lead has a lower melting point than the other constituents of the brass, it tends to migrate towards the grain boundaries in the form of globules as it cools from casting. The pattern the globules form on the surface of the brass increases the available lead surface area which in turn affects the degree of leaching. In addition, cutting operations can smear the lead globules over the surface. These effects can lead to significant lead leaching from brasses of comparatively low lead content.
Silicon is an alternative to lead; however, when silicon is used in a brass alloy, the scrap must never be mixed with leaded brass scrap because of contamination and safety problems.
In October 1999 the California State Attorney General sued 13 key manufacturers and distributors over lead content. In laboratory tests, state researchers found the average brass key, new or old, exceeded the California Proposition 65 limits by an average factor of 19, assuming handling twice a day. In April 2001 manufacturers agreed to reduce lead content to 1.5%, or face a requirement to warn consumers about lead content. Keys plated with other metals are not affected by the settlement, and may continue to use brass alloys with higher percentage of lead content.
Also in California, lead-free materials must be used for "each component that comes into contact with the wetted surface of pipes and pipe fittings, plumbing fittings and fixtures." On January 1, 2010, the maximum amount of lead in "lead-free brass" in California was reduced from 4% to 0.25% lead. The common practice of using pipes for electrical grounding is discouraged, as it accelerates lead corrosion.